Vitamin D3 Capsules from Lyphar is made of high quality Vitamin D, which is normally obtained from the diet or produced by the skin from the ultraviolet energy of the sun. The materials and methods for producing Vitamin D3 capsules typically involve several steps and ingredients. Here’s a general outline of what might be involved:
Materials of Vitamin D3 Capsules:
1.Vitamin D3 (Cholecalciferol): The active ingredient, usually sourced from lanolin (sheep’s wool) or fish liver oil.
2.Excipients: These are inactive ingredients used to formulate the capsule and ensure proper absorption, stability, and consistency. Excipients commonly include:
Fillers (e.g., lactose, cellulose): to add bulk and aid in the manufacturing process.
Binders (e.g., starches, cellulose derivatives): to hold the ingredients together in the capsule.
Lubricants (e.g., magnesium stearate): to prevent sticking of the ingredients to the manufacturing equipment.
Disintegrants (e.g., croscarmellose sodium): to help the capsule break down in the digestive tract.
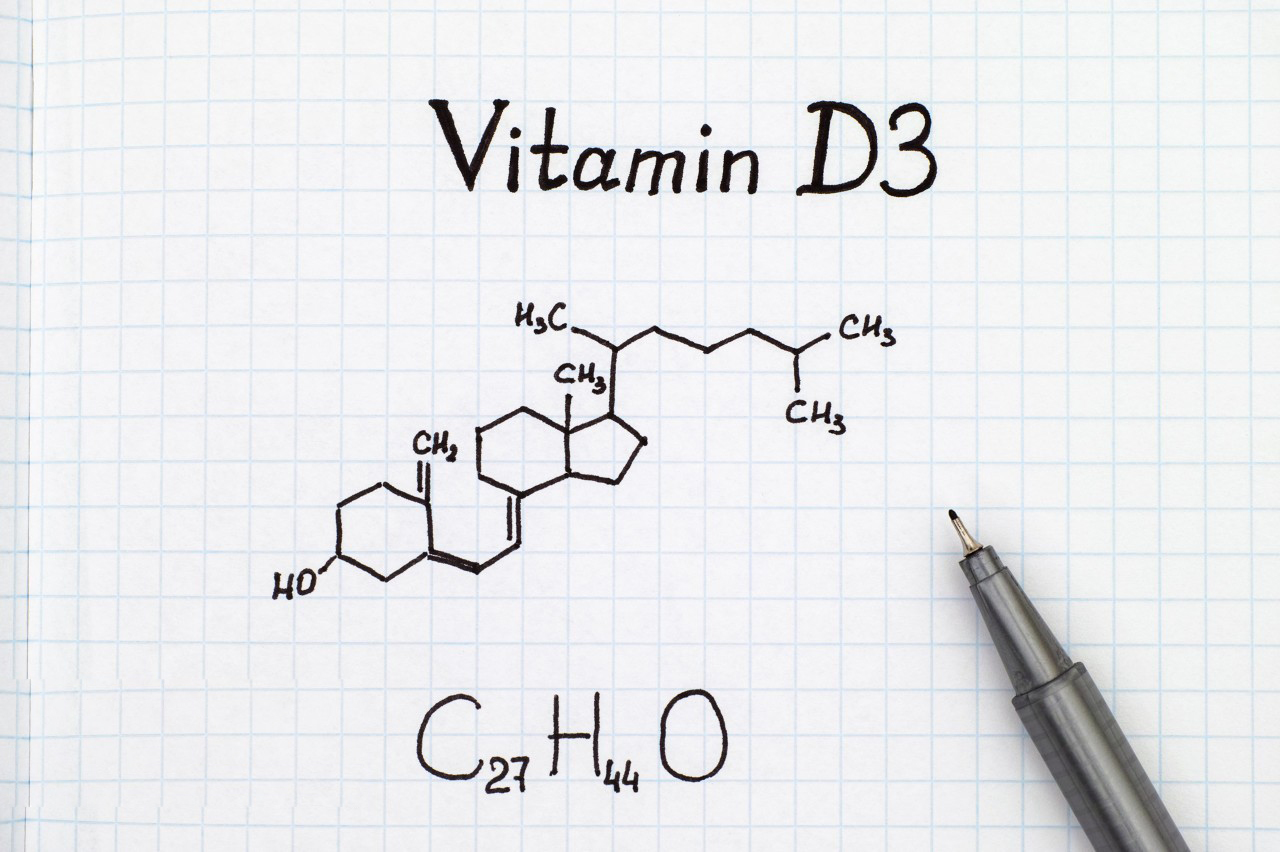
3.Capsule shells: Typically made of gelatin or a suitable vegetarian alternative like HPMC (hydroxypropyl methylcellulose).
4.Packaging materials: Bottles or blister packs for storing and distributing the capsules.
Methods of Vitamin D3 Capsules:
1.Formulation Development: Scientists and pharmacists determine the appropriate ratio of active ingredient to excipients based on factors like bioavailability, stability, and desired dosage strength.
2.Preparation of Excipients: Excipients are prepared according to their intended function. For example, fillers and binders may be mixed and granulated to ensure uniform distribution within the capsule.
3.Blending: The active ingredient (Vitamin D3) is blended with the excipients using specialized equipment to ensure thorough mixing.
4.Encapsulation: The blended mixture is then encapsulated using capsule-filling machines. Empty capsule shells are filled with the mixture, and then capped to seal the contents.
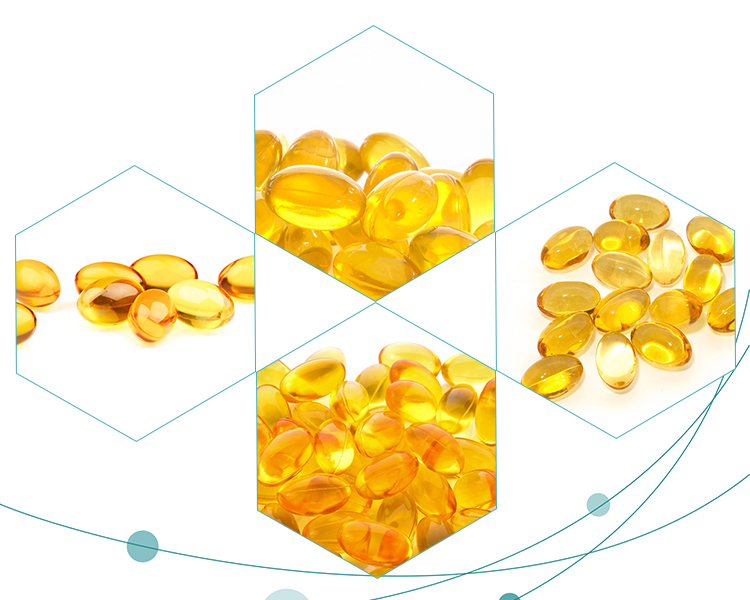
5.Quality Control: Throughout the manufacturing process, quality control measures are implemented to ensure the capsules meet specifications for potency, purity, and uniformity.
6.Packaging: Once filled, the capsules are packaged in appropriate containers, such as bottles or blister packs, and labeled with relevant information such as dosage instructions, expiration date, and batch number.
7.Storage: Finished capsules are stored under appropriate conditions to maintain their stability until they are distributed for sale.
It’s important to note that specific formulations and methods may vary depending on the manufacturer and regulatory requirements in different countries. Additionally, adherence to Good Manufacturing Practices (GMP) is essential to ensure the quality and safety of the final product.